AOI: Hypersonics
Innovation:
This project is designed to advance the state of the art in multi-material deposition for hypersonic applications and simultaneously drive expertise in multi-material solutions at Ohio universities. Arctos Technology Solutions expects to use this project to refine multi-material deposition developed within our R&D test beds – if successful this will help grow the Dayton-based OA group as experts in this rapidly growing AM focus area.
Objective:
The proposed effort will be to develop and validate specific processes for multi-material deposition, focused on real-world applications. The focus and objective of the effort will be to build parts for hypersonic devices with a thin shielding layer of refractory metal. This project will create gradient alloy parts with advanced laser powder bed fusion for hypersonic vehicles.
Background:
As the need for hypersonic devices increases, so does the demand for improved manufacturing processes. The extreme environment that hypersonic devices operate in severely limits the number of usable materials. The temperature regime approaches 2600°F and the only materials that can sustain their integrity are non-metals and refractory metals. Refractory metals have good thermal management properties and are a perfect choice for the hypersonic domain, but they are extremely dense and therefore not optimal for flight due to increase cost. Multi-material Additive Manufacturing (AM) provides the opportunity to have the best of both worlds - lightweight metals can be used for the building structure and a thin layer of refractory metals and be printed on the outside thus protecting the less thermally capable metals. While promising, this nascent technology has technical hurdles to overcome to be truly viable for hypersonic solutions. For example, creating a strong weld between the two materials is paramount otherwise the integrity of the whole system is in jeopardy, and validating that a process consistently produces a strong weld at the interface boundary requires thermal modeling and mechanical testing of specific multi-material processes.
Arctos Technology Solutions’ Open Additive group (OA) has been engaged in multi-material AM since 2016 when it was awarded contract# FA9453-17-C-0472 for graded alloys work. On that project, the OA team successfully implemented a multi-material deposition device and through the project, now has a background in selecting materials that are compatible to produce multi-material parts. On this effort, the OA group will design a refined multi-material deposition device that will be retrofitted onto the Laser Powder Bed Fusion (LPBF) test beds located at the University of Toledo (UT) and Ohio University (OU). Then with the guidance of OA, the universities will begin to use the Graded Alloys Process (GAP) to test material compatibility and create parts designs for hypersonic applications.
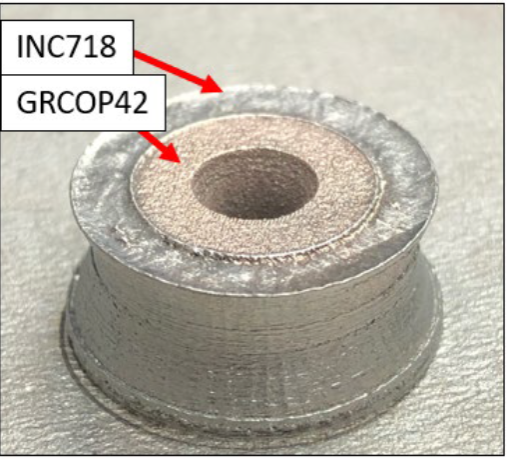