Innovation
The University of Dayton Research Institute (UDRI) and its partners (Ohio University, the University of Cincinnati, Wright State, and Youngstown State) have developed new tool fabrication methods based upon additive manufacturing, or "3D printing". The additive manufacturing methods developed will lead to the fabrication of complex geometry composite manufacturing tools with the fraction of the cost of conventionally machined metal tools. UDRI has demonstrated several complex aerospace quality tools that cost up to 70% less than a conventionally machined aluminum tool. Rapid composite fabrication methods utilizing tailored fiber placement (TFP) has reduced the fabrication time of advanced composites by over 50% while maintaining superior mechanical properties. Composite fracture toughness and delamination resistance was improved by 4X through incorporation of stitching in the TFP process.
Objective
To aid the Department of Defense (DoD) in trading these new composite fabrication and tooling technologies, Ohio University developed a non-proprietary cost model (ComCET) which provides a methodology for estimating the cost of manufacturing composite parts in a way that is accessible to a wide population of users. By implementing the methodology within Microsoft Excel, it utilizes an interface that will be familiar to users. Air Force Research Laboratory (AFRL) is planning to use this model to evaluate the cost savings attributes of future research and development programs as well by their financial staff in determine acceptability of cost proposals.
Background
The AFRL anticipates significant use of advanced composites in future unmanned aircraft. Unmanned aircraft are of interest to the DoD as reduced defense budgets combine to drive the need for new and innovative solutions that offer dramatic reductions in cost. To achieve the cost goals, significant reductions in the cost of fabricating composites are needed and one principal cost contributor is tooling for manufacturing composites.
Commercial Goal
This program has established over thirteen jobs amongst UDRI, the OFRN university partners, and other Ohio industry partners involved in this project. Ohio is rapidly becoming a national resource in additive manufacturing and this program aided Additive Engineering Solutions (Akron), Cincinnati Inc., General Electric Aviation, and Freshmade 3D (Youngstown). UDRI and these partners have seen over $3.3 million in new funding during this program and anticipate over $5M in the next few years supporting DoD UAV and hypersonics programs as well as commercial automotive composites development through IACMI.
UDRI has focused throughout this program in utilizing commercially available technologies; the TFP capability in Dayton is capable of fabricating over 16 ft2 composite preforms. UDRI, Freshmade, and AES all utilize COTS additive manufacturing techniques from Stratasys (FDM), Cincinnati Inc. (BAAM), and AMClad. Our partners are currently supporting several aerospace and automotive industry manufacturing technology development programs utilizing these technologies and are well postured for further research and manufacturing opportunities.
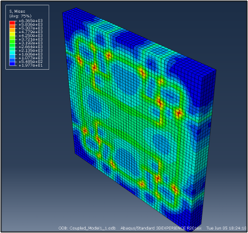