Innovation
The proposed generator and advanced non-linear controller would be an enabler of directed energy weapons (e.g. lasers), which are fundamentally more precise and less expensive to operate than their traditional counterparts but are susceptible to large and potentially harmful transients.
Objectives
This project seeks to increase the power density, the controllability, the reliability, and the manufacturability of HVDC generator systems. The four work packages, detailed below, focus on addressing these four technical challenges, respectively.
- High-Speed, HVDC Generator Rotor: Higher-rotor speeds enable higher power density generators, but presents major stress and rotor stability challenges, and requires highly engineered tradeoffs between structure and electromagnetics.
- Advanced Non-Linear Controls: Aircraft AC and HVDC generators are both based on 3-stage, wound-field, synchronous designs. Generator output voltage is regulated by the GCU changing the power level of the electromagnets on the rotor. Traditional GCUs have uni-directional output voltage to increase power using only two power electronic switches. The proposed GCU will use four switches to allow bi-directional voltage, both to increase and decrease generator output. Additionally, using the advanced non-linear controls with this bi-directional GCU will significantly reduce the response time to electrical load changes. Simulations show a 60% reduction in response time is possible.
- Thermal Modeling: The Generator Cooling Circuit and Rectifier Heat Sink Thermal design are core to achieving reliable generators with a high-power density. The objective is to remove the vast amount of heat generated during the conversion of AC to DC power as reliably, efficiently and cost effectively as possible.
- Large Generator Housing Fabrication and Industrialization: Large oil-cooled generators have complex castings that create weight, reliability, and quality challenges. Advanced manufacturing methods can address these topics as well as decreasing the development costs and the lead-times for the tooling and the parts themselves.
Background
This project seeks to develop an advanced high-voltage direct-current (HVDC) oil-cooled generator system with rapid dynamic response for US military aircraft. These generator systems will operate at higher speed and power level, with improved reliability and controllability. This development effort supports the Air Force Research Laboratory (AFRL) and NASA-Glenn Research Center electrical power system and propulsion road maps and furthers an AFRL goal to see more robust competition and innovation for electrical power systems. Required electrical power levels are growing on all aircraft types as electrical systems replace hydraulic controls and power de-icing, as well as engine start, and other critical functions. For military aircraft, the growing use of radar systems, electronic jamming, and directed energy weapons (lasers) are driving the exponential growth in electrical power needs. Most recently, novel aircraft architectures are taking advantage of hybrid electric propulsion technologies for lift, thrust, and enhanced engine control. Although HVDC generators predominantly use much of the same technology as traditional alternating current (AC) generators, their development still presents some significant challenges that we will solve for. Since electrical frequency is not a limiting factor for direct current (DC) generators, they can spin much faster to achieve higher power with less weight. The mechanical rotor design must be optimized to handle these high speeds and associated stresses. Second, directed energy weapons and radar loads drive the need for advanced controls to regulate voltage in the face of large and potentially harmful transients. Third, the generators must internally convert AC to DC power with a rectifier module, which produces significant heat that must be removed. Lastly, the increasing size of generators requires advanced manufacturing processes and capable supply chains to ensure that large, complex housings with internal oil cooling passages are durable and reliably manufacturable.
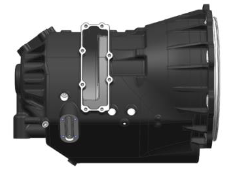