Santa Maria, CA – The aerospace industry is on the cusp of a revolutionary transformation, supported in part by the Ohio Federal Research Network's (OFRN) $1,193,345 investment in a cutting-edge space manufacturing project. This project “Structural Materials Joining in Space” focuses on the feasibility of laser welding in space and represents a significant leap forward in our ability to manufacture and repair structures beyond Earth. The project is a collaborative effort involving researchers and scientists from The Ohio State University (Ohio State), the Air Force Research Laboratory (AFRL), the National Aeronautics and Space Administration (NASA), and other industry partners.
A New Frontier in Space Manufacturing
In late August 2024, the Ohio State LUNARWELD Team – along with engineers & scientists from NASA Marshall Space Flight Center (MSFC) -- traveled to Santa Maria, California, where they conducted parabolic flights to simulate microgravity and lunar gravity conditions in a vacuum chamber. The project aims to test and refine welding techniques in space-like conditions. The parabolic flights were carried out by Zero-G Corporation using a specially modified Boeing 727, which provided the Ohio State team with the means to conduct their experiments and collect data for their research into space welding technologies. NASA MSFC, NASA’s Space Nuclear Propulsion program, NASA Science Mission Directorate’s Biological and Physical Sciences Division, and NASA Space Technology Mission Directorate’s Flight Opportunities program funded this set of parabolic flights.
Eugene Choi, a graduate student at Ohio State, said, “We are trying to understand the capability of laser welding in a space-like environment. This involves simulating the vacuum of space and the microgravity and lunar gravity environments using a parabolic flight.”
Photo caption: Ohio State student Eugene Choi adjusts the vacuum chamber.
Photo caption: Ohio State student Aaron Brimmer adjusts the laser platform inside the vacuum chamber.
This project began as a senior capstone and has evolved into a two-year research effort. The team is leveraging a retrofitted vacuum chamber developed by NASA Langley Research Center and a 1kW laser to perform various welding tests in simulated space conditions. The team is testing welding techniques on aluminum, stainless steel, and titanium alloys, which are commonly used in aerospace applications.
“Our goal with this project is to kickstart welding in space,” Choi said, “and it’s aligned with NASA's focus on in-space manufacturing.”
Photo caption: View inside the vacuum chamber of the laser beam and testing platform.
Photo caption: Laser experimentation result.
The Challenge of Microgravity, Lunar Gravity, and Vacuum Conditions
To simulate space conditions, the team is using a modified Boeing 727 provided and operated by Zero-G Corporation under contract with NASA to conduct parabolic flights. During these flights, the aircraft ascends to a high altitude before descending rapidly to create brief periods of microgravity. Each parabola provides approximately 15 to 20 seconds of zero gravity, which is the time allotted for conducting the welding experiments. The plane is also capable of conducting shallower parabolas to provide Lunar gravity conditions.
To ensure safety and health during the flight tests, students are preparing by securing all equipment and conducting thorough checks. For personal safety, they are adapting to the high-G environment of the aircraft by positioning themselves flat on the floor during the initial ascent to prevent disorientation and nausea. Additionally, they are managing the thermal conditions of the equipment carefully, with temperature monitoring to prevent overheating and potential damage to sensitive components.
Will McAuley, an Ohio State graduate student involved in the project, explained, “On the ground, we’re replicating the conditions we’ll face in space by testing various welds and materials. It’s like a rehearsal for the real performance to ensure everything is perfect before we take this in zero gravity.”
Photo caption: Ohio State students Aaron Brimmer (left) and Will McAuley (right) setting up the vacuum chamber inside the Zero G Boeing 727.
The experimental setup is planned to ensure the integrity of the equipment during the flight. The vacuum chamber and other apparatus are securely fastened, and sensitive electronics are protected to prevent damage during the high-G ascent and microgravity and lunar gravity phases.
Key Contributions from AFRL and NASA
The AFRL plays a pivotal role as the technical point of contact and government champion for this project.
Dr. Arlene Smith, a research materials engineer at AFRL, said, “This is an innovative technology that will drive our research forward into the realm of in-space manufacturing. It’s at the cutting edge of science and technology, taking us to a whole new frontier.”
Photo caption: Ohio State Professor Dr. Antonio Ramirez, Air Force Research Laboratory Materials Engineer Dr. Arlene Smith, and Ohio State Assistant Professor Boyd Panton on the Santa Maria Airport tarmac in front of the Zero G Boeing 727.
NASA’s involvement is important in providing hardware, expertise, and funding the flights themselves. Dr Andrew O’Connor, a materials scientist at NASA Marshall Space Flight Center, is coordinating NASA’s contribution to the experiment's execution.
He said, "We are using a vacuum chamber originally developed by NASA Langley Research Center to conduct the experiments. Our role includes integrating advanced laser welding technology into this chamber, which was previously equipped for electron beam additive manufacturing. This integration is important for adapting the chamber to meet the specific needs of our microgravity and Lunar gravity simulations."
O'Connor says that the chamber, which was last used in a microgravity flight in 2007 by NASA, required significant upgrades to accommodate the new equipment and experimental conditions for the Ohio State Lunar Weld Team’s experiment. These upgrades were funded by the Ohio Federal Research Network and NASA Marshall Space Flight Center.
The Role of Ohio State and Future Plans
Ohio State professors and students have been integral in adapting the vacuum chamber and developing the experimental protocols.
Dr. Antonio Ramirez, a professor at Ohio State, said, “We are investigating how welding performs under extreme conditions—vacuum, microgravity, and eventually lunar gravity. This research is important for advancing space construction and repair technologies, and we aim to make space manufacturing more feasible and efficient as a result.”
Photo caption: Ohio State professor Dr. Ramirez, sets up the vacuum chamber inside the Boeing 727.
The results from these experiments are expected to provide valuable data for developing computer simulations of welding in space. These simulations could eventually allow for predictive modeling of welding processes, reducing the need for costly physical experiments in space.
The Role of Zero G
Photo caption: Zero-G’s modified Boeing 727 aircraft.
Zero-G Corporation, a commercial company specializing in microgravity flights, provides the modified Boeing 727 aircraft and manages the logistics of performing parabolic flights.
As Dr. O’Connor explains, “Zero G reviews our technical readiness, ensuring our equipment is properly installed and operates safely during the flights. They perform exhaustive checks to address any potential hazards and ensure a smooth operation.”
The FAA also plays an essential role by overseeing the safety and regulatory compliance of the parabolic flights. The agency ensures that the modified aircraft used for the experiments meets all safety standards and is equipped to handle the unique demands of simulating zero gravity.
The project also involves intricate technical preparations led by the Ohio State students. The vacuum chamber must be precisely calibrated, and all hardware must be compatible with the unique conditions of parabolic flight. The experimental setup includes various sensors and cameras to monitor the welding process within the vacuum chamber, gather data, and ensure that the conditions inside the vacuum chamber are as close to what is experienced in space as is possible.
Sarah Huetter, an electrical engineering student on the Ohio State capstone team, said, “I’m responsible for ensuring the electrical systems function correctly during the flights, particularly monitoring temperatures to prevent any damage to sensitive equipment. We need to keep the camera systems below their maximum rated temperature to avoid any malfunctions or melting and ensure we capture the weld process.”
Photo caption: Ohio State students (left to right) Grant Smith, Sarah Huetter, and Eugene Choi pose for a photo before their flight in front of the Zero G Boeing 727 on the Santa Maria Airport tarmac.
Looking Ahead
The team plans additional testing in the winter or fall of 2024. They will use the insights gained from these upcoming experiments to refine their methods and improve the technology. This ongoing research is set to significantly advance space exploration by making the construction and repair of complex structures in space more cost-effective.
Photo caption: Ohio State student Eugene Choi sets up the vacuum chamber inside the Boeing 727.
Eugene Choi said, “I’m incredibly fortunate to be at the forefront of a groundbreaking industry. This research isn't just about pushing boundaries; it’s a pivotal leap towards constructing structures on lunar surfaces and beyond, shaping the future of space exploration. I’m deeply grateful to be part of this project—it means everything to me to contribute to something that could fundamentally change how we explore and utilize space.”
Sarah Huetter also said, “Being part of this project has truly realized my dream of working with NASA. It's an incredible opportunity to be involved in this research that could redefine space manufacturing. Every challenge and learning moment here is a testament to how far we’ve come, and I’m deeply grateful for the chance to contribute to this effort.”
As this research continues to push the boundaries of what's possible in space manufacturing, it highlights the importance of collective effort and visionary thinking.
Maj. Gen. (ret.) Mark Bartman, VP for Advanced Development at Parallax Advanced Research supporting the Ohio Federal Research Network, said, “This project embodies the spirit of innovation and collaboration necessary to advance humanity's presence in space and sets the stage for a new era in aerospace manufacturing. Parallax and the OFRN are honored to be a part of it.”
###
About Parallax Advanced Research and the Ohio Aerospace Institute
Parallax Advanced Research is a 501(c)(3) private nonprofit research institute that tackles global challenges through strategic partnerships with government, industry, and academia. It accelerates innovation, addresses critical global issues, and develops groundbreaking ideas with its partners. With offices in Ohio and Virginia, Parallax aims to deliver new solutions and speed them to market. In 2023, Parallax and the Ohio Aerospace Institute formed a collaborative affiliation to drive innovation and technological advancements in Ohio and for the nation. The Ohio Aerospace Institute plays a pivotal role in advancing the aerospace industry in Ohio and the nation by fostering collaborations between universities, aerospace industries, and government organizations, and managing aerospace research, education, and workforce development projects.
About Ohio Federal Research Network (OFRN)
The OFRN has the mission to stimulate Ohio’s innovation economy by building statewide university-industry research collaborations that meet the requirements of Ohio’s federal laboratories, resulting in the creation of technologies that drive job growth for the State of Ohio. The OFRN is a program managed by Parallax Advanced Research in collaboration with The Ohio State University and is funded by the Ohio Department of Higher Education.
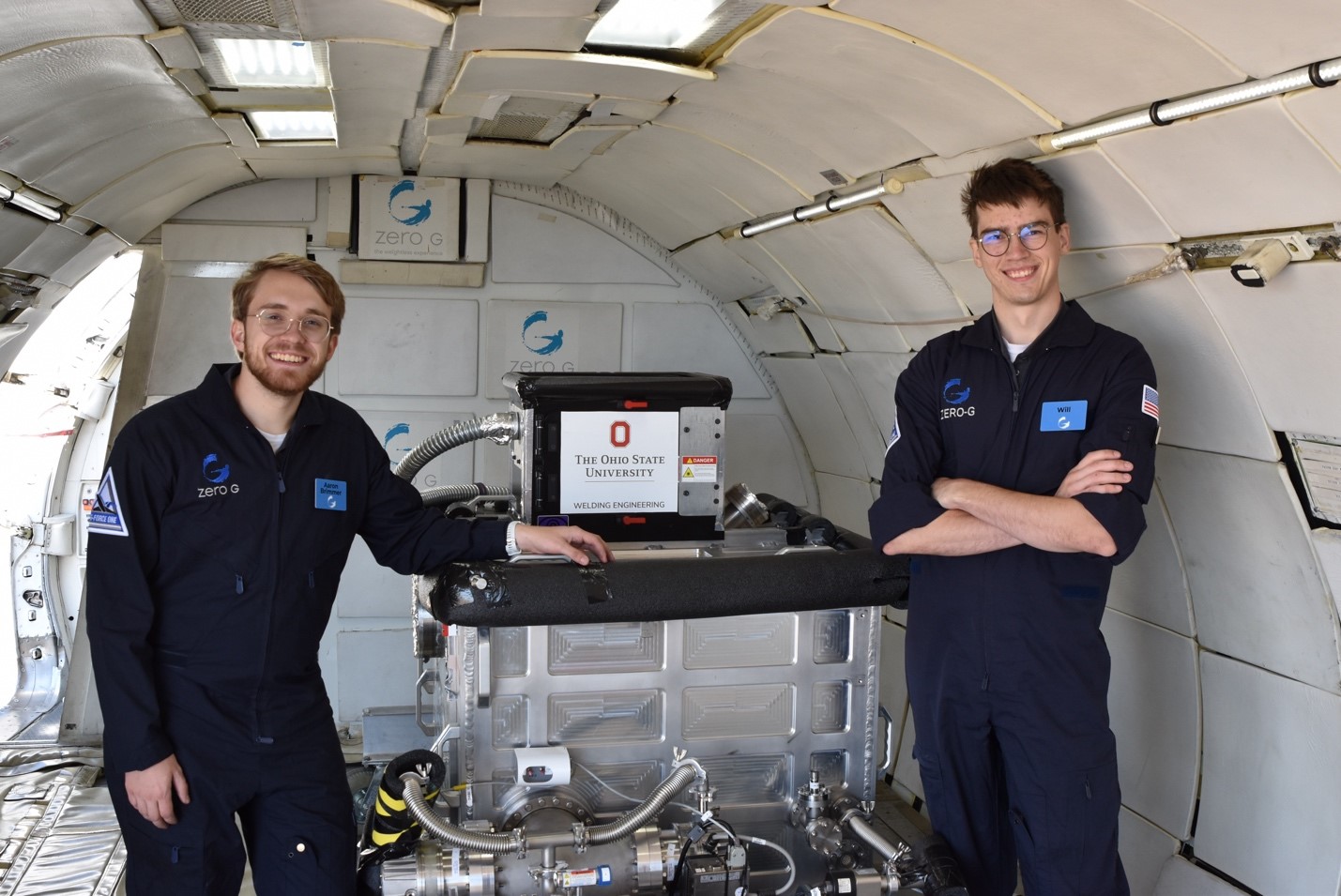